High-Velocity Oxygen Fuel, or HVOF Gun, is a thermal spray coating method used to coat surfaces with a variety of materials to improve their qualities. In order to produce a dense and adherent coating, this method combines high-velocity gases with tiny powder particles. Excellent wear resistance, corrosion resistance, and other desired qualities are common in coatings made by HVOF.
The convergent-divergent nozzle is used to steer the rapidly expanding combustion gases. The gases are accelerated to supersonic speeds by this nozzle design, producing a high-velocity jet of hot gases. Just as the gas stream is about to leave the nozzle, the coating material is injected as a powder. The ceramic powder particles are carried by the fast gas, which accelerates them to very high speeds.
Powder particles that have been propelled strike the substrate with a lot of kinetic energy. The particles distort, melt, and attach to the substrate surface upon impact, creating a covering that is dense and firmly adhered. The molten particles quickly solidify and produce a solid coating layer as the coated substrate rapidly cools as it travels away from the cannon. HVOF coatings have a number of benefits, including as superior adhesion, less porosity, and enhanced mechanical qualities.
Types of Technology In HVOF
In comparison to conventional thermal spray technologies, the high particle velocities and regulated combustion process provide coatings with reduced oxide content and enhanced density. Furthermore, the HVOF’s comparatively moderate process temperatures aid in maintaining the ideal coating materials’ characteristics.
HVOF coatings are used in a variety of sectors, including oil and gas, aerospace, automotive, and power generation. Metals, ceramics, and cermets (ceramic-metal composites) are the most typical coating materials utilized in the HVOF process. The unique needs of the application, such as wear resistance, corrosion resistance, heat protection, and more, determine the coating material to be used. HVOF is a flexible and efficient technology for creating superior-performing coatings of the highest caliber.
Applications of HVOF
- HVOF coatings are used on turbine blades, vanes, and other engine components to improve wear resistance, thermal barrier properties, and overall component lifespan. Coatings on landing gear components help resist wear and abrasion caused by repeated landings and takeoffs.
- HVOF coatings are applied to engine cylinder liners, piston rings, and valves to enhance wear resistance and reduce friction, leading to improved fuel efficiency and engine performance. Coatings on exhaust components provide corrosion resistance and thermal protection against high temperatures.
- Drilling tools with HVOF coatings have increased wear resistance, prolonging their operating life in challenging drilling conditions. Coatings are employed to shield pipeline parts from corrosion, erosion, and abrasion brought on by the fluids being transported. Gas turbine parts with HVOF coatings are more durable and efficient overall because they are more resistant to high-temperature oxidation and erosion.
- Coatings on the blades and other parts of steam turbines increase dependability by reducing wear and acting as a thermal barrier. HVOF coatings extend tool life, lessen wear, and increase machining performance on cutting tools including drills, end mills, and inserts. Rollers used in various production processes have coatings to increase wear resistance and prolong roller life.
- HVOF coatings protect items like buckets, blades, and crushers from abrasion and wear, increasing the lifespan of mining machinery. By shielding against corrosive agents and abrasive particles, coatings on valves and pipe components provide increased service life and reliable operation. Through the prevention of corrosion and marine fouling on ship propellers, shafts, and rudders, HVOF coatings increase vessel efficiency and maintenance intervals. HVOF coatings improve patient outcomes by increasing the biocompatibility and wear resistance of medical implants including hip joints and knee replacements. HVOF coatings can provide electrical insulation and temperature management for components used in semiconductor production processes.
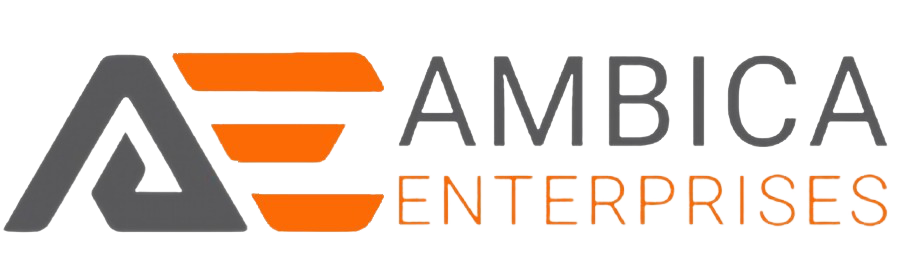
- Call Us - +91 74138 97813
- Whatsapp - +91 74138 97813
- Address - 324-25, 378-79-80, khasra No. 9/4, Shree Yade Gaun, Banar Ring Road, Jodhpur, Rajasthan 342027